Production and Client Orders in OPTO may be placed on hold – this will remove the allocation of materials and will stop the order from being despatched. The Employee will require permission and an internal employee password set-up in their employee record. (see below)
From the OPTO ribbon, select the ‘Resources’ tab and click on the ‘New/Edit Employee’ icon to open the ‘Employee Details’ window. Enter a password in the Password field then select the ‘Security’ tab and click in the ON-HOLD (Clt)and the ON-HOLD (Prd) boxes to tick (circled below).
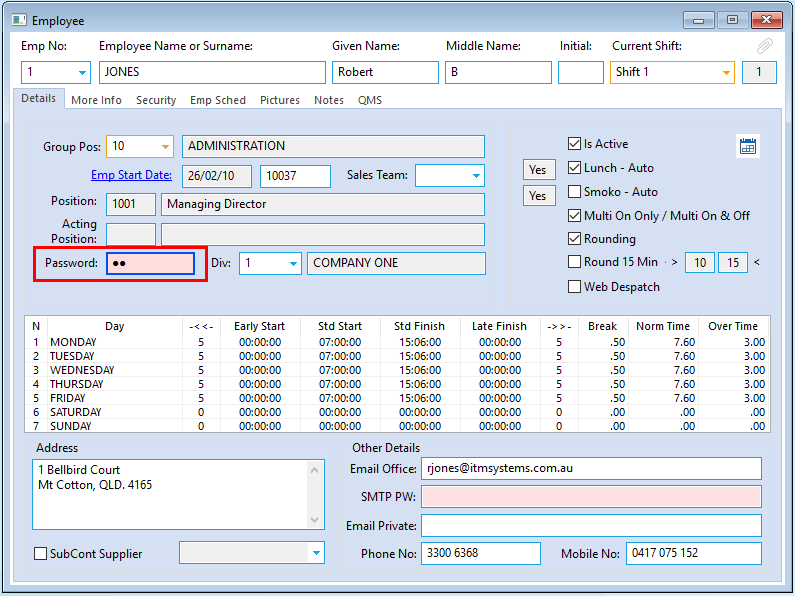
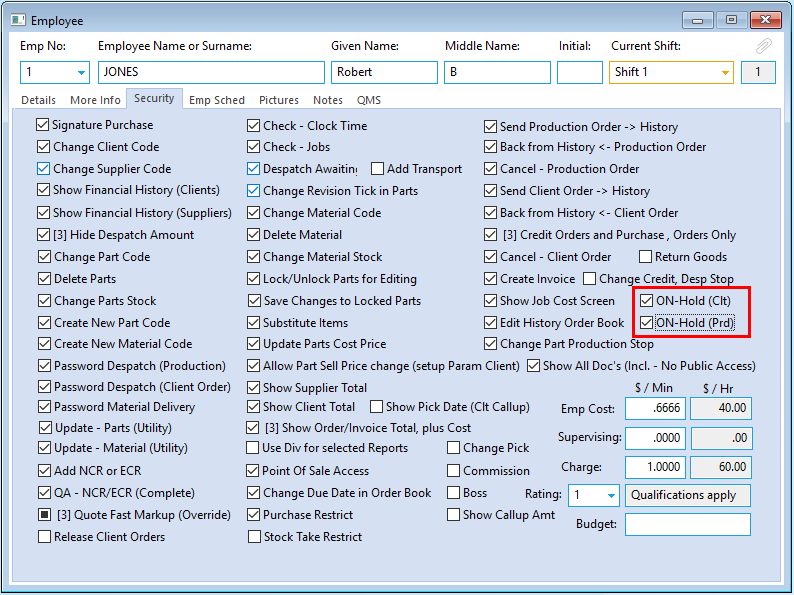
To Place a Production Order On-Hold
From the OPTO ribbon, select the ‘Orders’ tab and click on the ‘Edit Factory Order’ icon (1). In the Order No field press <F2> and select the order from the pop-up list then click on OK. Press <TAB> to generate the window, click on the ‘Despatch’ tab and click in the ‘Order on Hold’ box to tick (2). Enter the internal employee password, click on the OK button, and press <F9> to save.
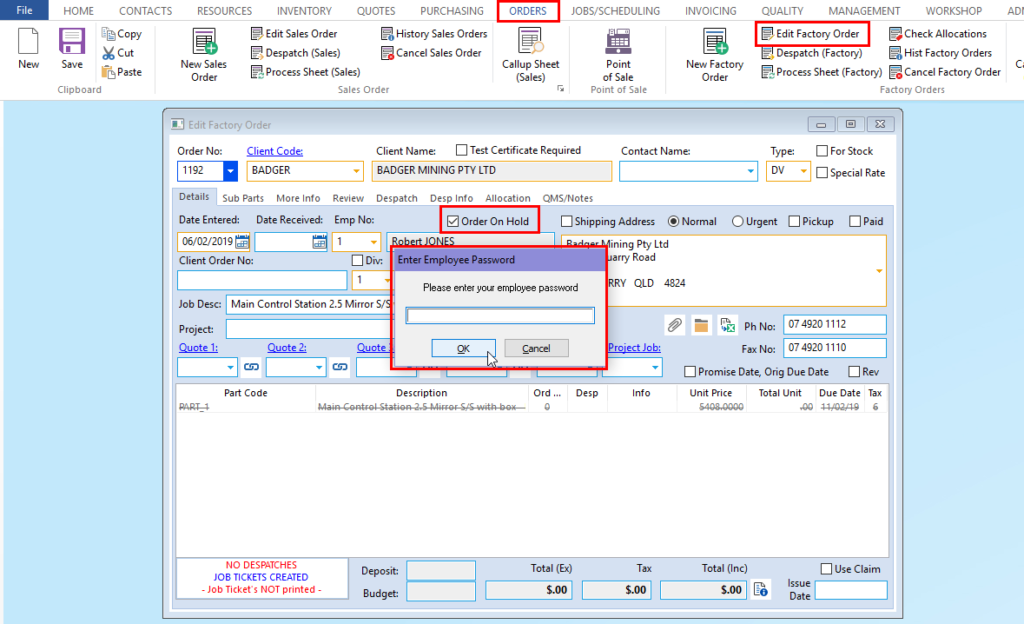
To Place a Client Order On-Hold
From the OPTO ribbon, select the ‘Orders’ tab and click on the ‘Edit Sales Order’ icon (1). In the Order No field press <F2> and select the order from the pop-up list then click on OK. Press <TAB> to generate the window, ensure to click in the OnHold box to tick (2) then press <F9> to save.
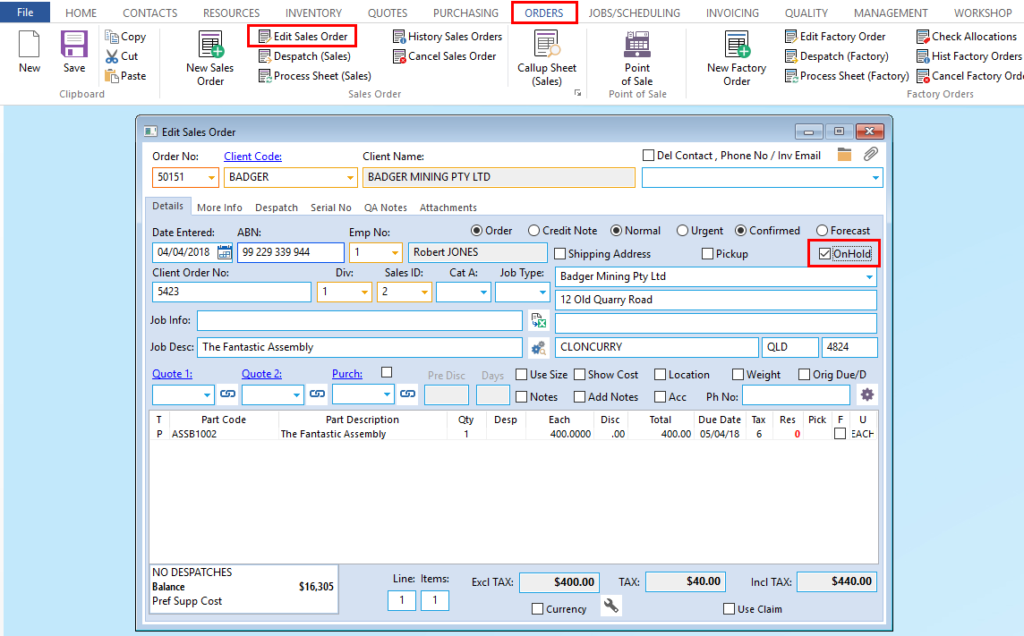
The message pane on the ‘Details’ tab of the orders alerts USERS that the order is on hold. (See below)
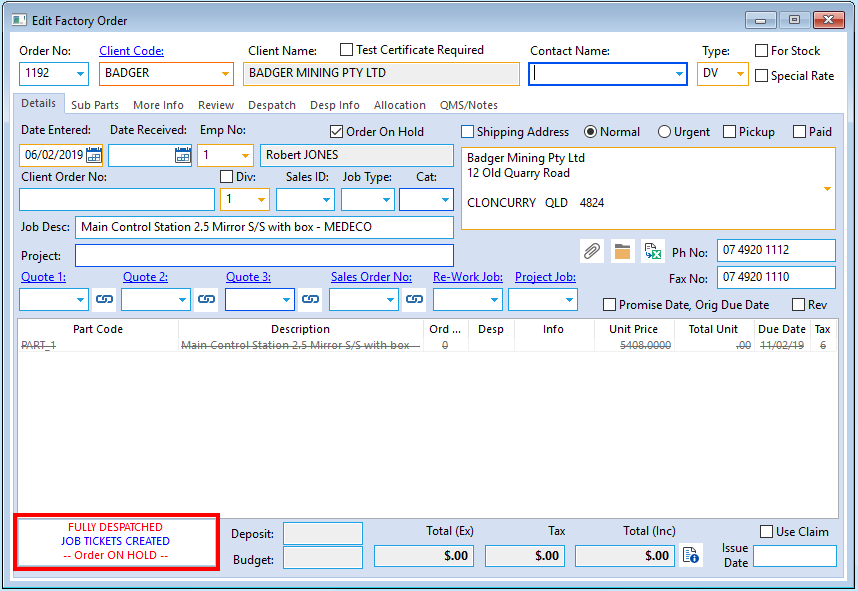
The Order cannot be despatched while it is On Hold.
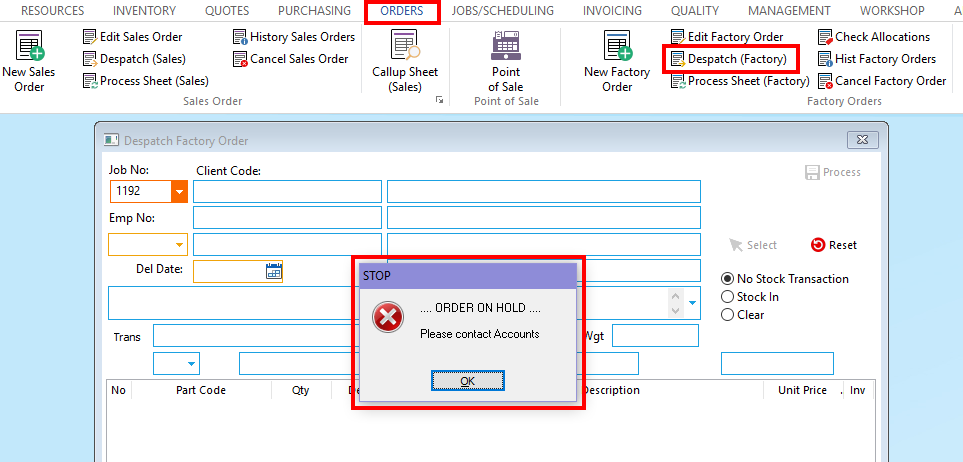
To Remove the On-Hold Feature on a Production Order
From the OPTO ribbon, select the ‘Orders’ tab and click on ‘Edit Sales Order’ or ‘Edit Factory Order’ then click in the OnHoldbox (Sales Order) or the Order On Hold box (Factory Order) to un-tick. Enter the internal employee password where required then click on OK and press <F9> to save. USERS can now despatch the orders as normal.
Opto Software Pty Ltd Revised 03/08/2018